Forecasting failure
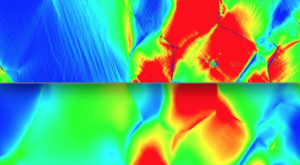
Top: a high-resolution digital image correlation, a technique that measures strain that shows on the surface of a specimen, in this case tantalum oligocrystal. The colors correspond with the magnitude of the strain, with blue lowest and red highest. Bottom: The predicted strain for the same sample as simulated via crystal plasticity finite element modeling. The prediction agrees well with the measured strain. (Images: Sandia National Laboratories.)
Welders have known for centuries that when they connect two pieces of cast metal, the joint is susceptible to splitting, cracking, buckling – failure. Experience and testing can lower the risk, but welding imperfections mean the potential for failure is ever present.
When the consequences of weld failure could be catastrophic – mid-flight, say – minimizing that risk is paramount. But predicting failure in various real-world scenarios remains based on experience and conjecture.
“When a manufacturer says, ‘we made some welds and got N-number of pores in there, is that OK?’ the answer to that question currently is, ‘I don’t know,’” Sandia National Laboratories’ Brad Boyce says. Boyce is co-principal investigator of the Predicting Performance Margins (PPM) program, a lab initiative to bring science-based predictive capabilities to questions of material strength and reliability.
Now in its fifth year, PPM is closing the gap between atomic-scale modeling and bulk materials behavior by exploring physics at the micrometer scale. This intermediate, or mesoscale, science is the least understood aspect of material properties. Engineers expect mesoscale advances will help them move beyond validation of material performance and toward accurate prediction and control in the design process. It offers clues as to how impurities affect crystal formation and how crystal structure deformations lead to the resulting bulk-scale materials behavior under working conditions.
At the micrometer scale, the PPM team combines high-performance computing with novel experiments to explore the pores, divots, gaps and other imperfections that weaken a weld joint or polymer seal.
In a 2015 proof-of-concept study in the International Journal of Mechanical Science, the PPM team used some of the highest-resolution metallic-grain-deformation data published to date to demonstrate that its experimental results and computational models align quantitatively.
This technical achievement required innovative approaches to both the experimental system and the calculations. When scientists want to analyze crystalline grains in a metallic sample at the mesoscale, they usually subject it to various applied strains and then use a scanning electron microscope to measure changes in the crystal structure. Since the instrument collects only surface data, scientists can only infer what’s happening inside a sample. The Sandia team developed a heat treatment to form tantalum oligocrystals with large, one-millimeter grains that spanned the entire width of the sample, creating a monolayer that made surface measurements possible. The researchers also created a customized loading stage coupled with a high-resolution digital image correlation method that let them collect detailed data from the entire sample.
“By making the grains a millimeter in size we get extremely good resolution that was not possible previously,” Boyce says.
On the computational side, postdoctoral scientist Hojun Lim worked with co-principal investigator Corbett Battaile to perform simulations that closely matched the experimental conditions. They built a crystal plasticity model that described the evolution and propagation of dislocations using continuum state variables and coupled that model with Sandia’s Sierra Solid Mechanics multi-physics code, which was developed as part of the Advanced Simulation and Computing (ASC) program.
“Without those resources in place we would not have been able to pull off what we did,” Battaile says. “The minute details of how you treat the material in comparison to the model, making sure you have the exact same geometry that you have in the experiment, that you have the same force field and boundary conditions, all the little details can make a really big difference.”
To compare measured and simulated results, the researchers mapped experimental data to the model’s finite element mesh. Model predictions of both surface strains and grain rotations at a range of applied strains matched experimental results well enough to validate the computational model.
“We think of bulk materials as having some percent ductility, but the reality is that these materials have a variability of properties,” Boyce says. “The sources of that variability are in the microstructure. Now that we can trust our model, we can start to run hundreds of microstructural simulations and get distributions of behavior and ultimately elucidate the worst cases of microstructure that cause the worst behavior.”
The team can begin to answer this question: Will it hold? And nowhere is that quandary more pertinent than in 3-D printing or, as it’s known in industry, “additive manufacturing.” Sandia engineers have been among the pioneers in the field, developing Laser Engineered Net Shaping (LENS), a process to print complex metal parts from powders poured into molds and fixed by laser energy. Manufacturers are excited about the potential of this process, but many questions remain about its performance under the stringent standards required for an airplane or, say, as a replacement part destined for the nuclear stockpile.
“Our challenge is to understand the deformation and failure of these materials,” Boyce says.
“From a manufacturing perspective, this additive method bears some very important similarities to laser welding, which is our model. From a materials science standpoint, it has awkward microstructure grains and porosity and questions about how much porosity you can tolerate.
“We are able to use the infrastructure from PPM to hit the ground running on this problem of what is the influence of microstructure and defects on the structural reliability of these parts.”
A shorter version of this article appears in the current issue of Stewardship Science magazine, the annual publication of the DOE National Nuclear Security Administration Stewardship Science Graduate Fellowship.
About the Author
Karyn Hede is news editor of the Nature Publishing Group journal Genetics in Medicine and a correspondent for the Journal of the National Cancer Institute. Her freelance writing has appeared in Science, New Scientist, Technology Review and elsewhere. She teaches scientific writing at the University of North Carolina, Chapel Hill, where she earned advanced degrees in journalism and biology.